INHABITR LUXURY FURNITURE RENTALS
RETAIL
LEVERAGE END-TO-END VISIBILITY TO OPTIMIZE WAREHOUSE OPERATIONS
AUTOMATE FURNITURE SHIPPING RECEIVING VALIDATIONS, ELIMINATE RERUNS
INTHING’S RETURNABLE ASSET TRACKING SOLUTION + ZEBRA RFID READERS
BUILT FOR FF&E SUPPLY CHAIN. OPTIMISED OPERATIONAL EFFICIENCY, REDUCED CARBON FOOTPRINT
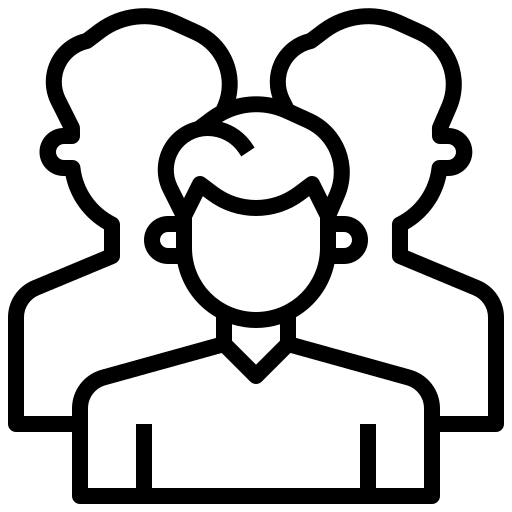
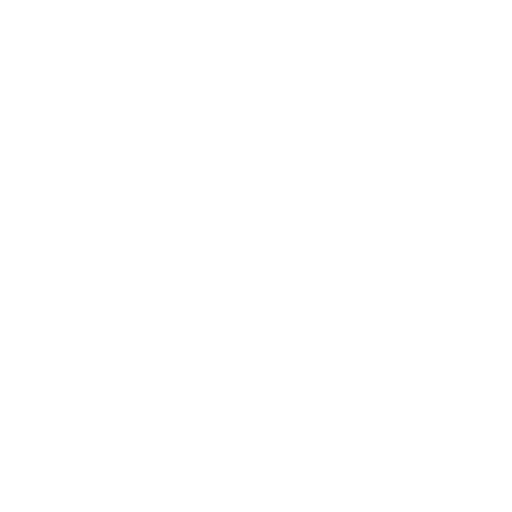
Customer
Inhabitr Furniture Rentals
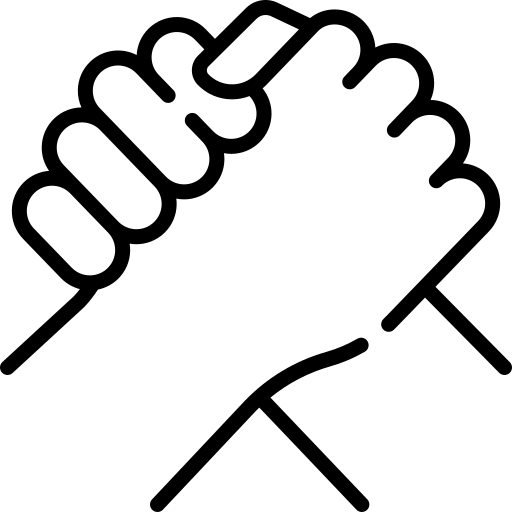
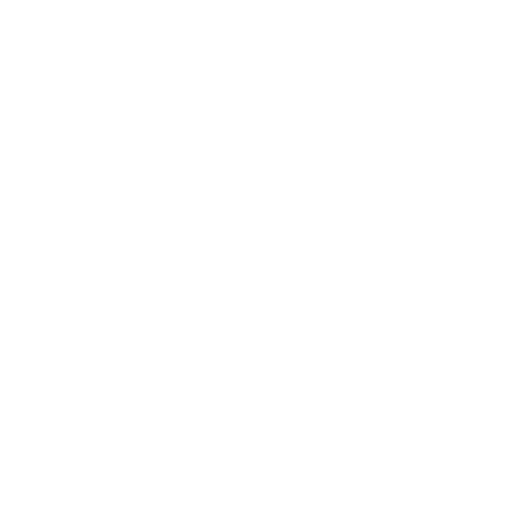
Partner
Zebra
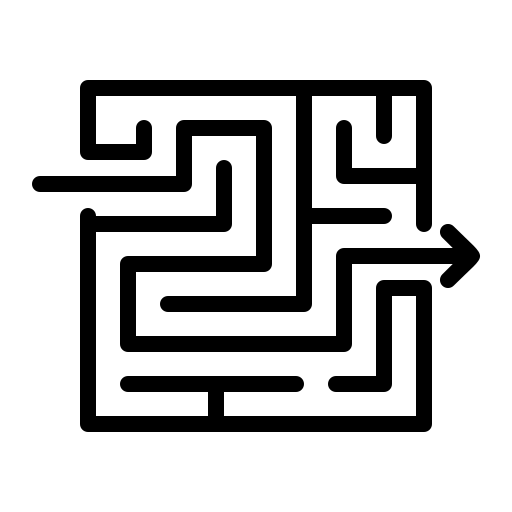
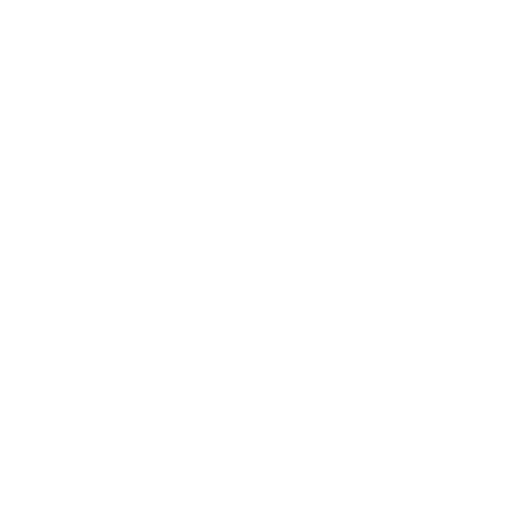
Challenge
Inefficient use of time, and human errors in locating, inventorying, picking, packaging, shipping, auditing & receiving operations in their furniture warehouses thereby increasing the transit time.
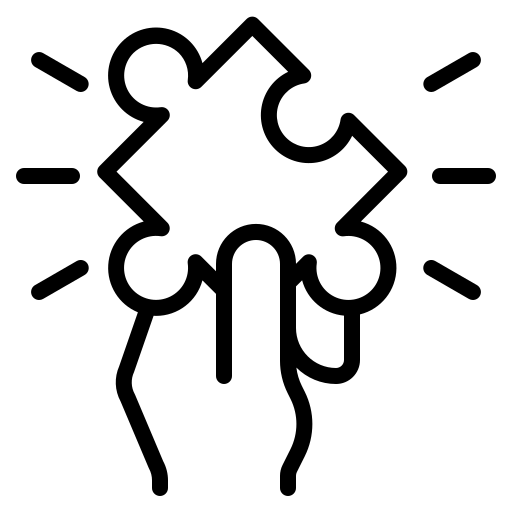
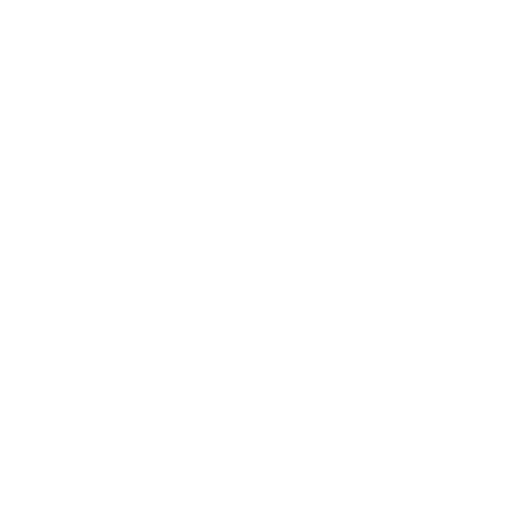
Solution
Zebra Handheld & Fixed RFID Readers, Zebra A5060 & A5010 antennae, RFID & GPS tags, InThing’s Returnable Asset Visibility Software
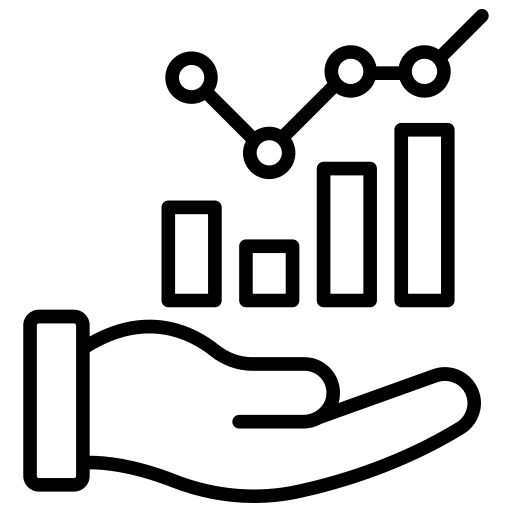
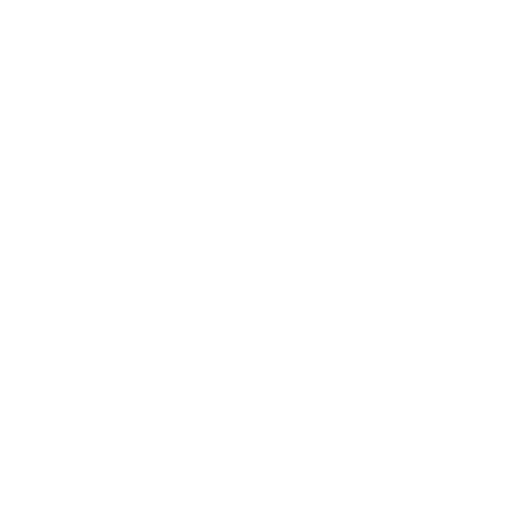
Results
Significantly enhanced operational efficiency at a price-point of $18 per day per dock-door. Helped the warehouses automate shipping receiving validations to prevent wrong shipments, eliminate re-runs between warehouses and customer locations, and accurate updation of inventory audit records. Overall, the increased visibility provided unparalleled flexibility, enhanced speed of delivery and better cost efficiency.
The challenges of an AI-powered furniture rental platform
A pioneering luxury furniture rental company using AI to customize furniture choices, specific designs, accents and furnishing arrangements did not have a cutting-edge sensor solution trained for FF&E supply-chain, to help it scale up or down based on changing business needs while affording accuracy, speed and cost efficiency. With furniture rentals running into thousands of units, it was critical to know whether the chosen furniture sets reached specific locations for specific customers. Manual, paper-based process to conduct inventory checks and locate specific furniture items within a large warehouse was proving cumbersome, while audit and reconciliation of inbound furniture items was labor intensive and incomprehensive.
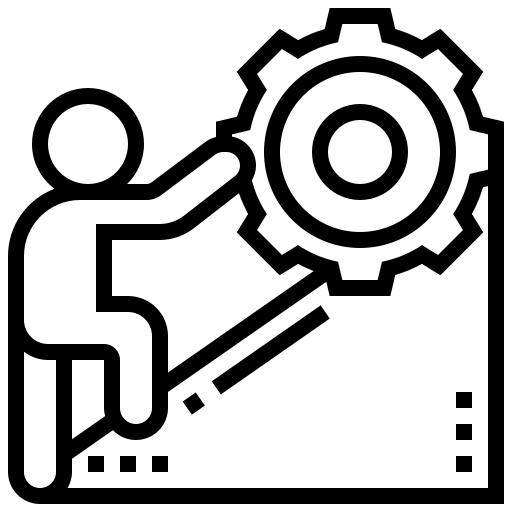
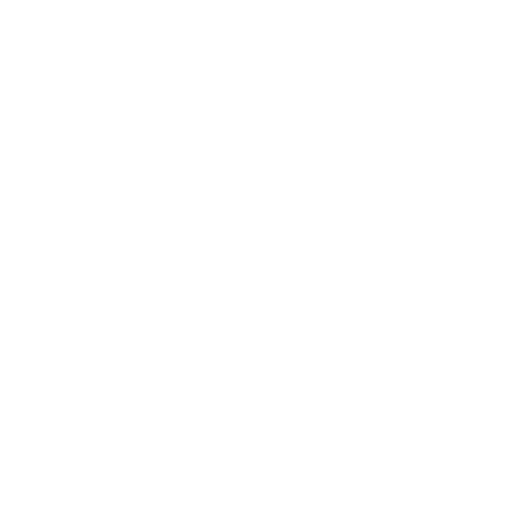
Existing Challenges
♦ A pioneering AI powered FF&E furnishing platform was using manual, paper-based processes to conduct inventory checks & locate furniture within large warehouses.
♦ Warehouse personnel had to deal with lack of visibility in accurately knowing location of chosen furniture sets, whether they had reached the customer and were returned and received.
♦ There was significant time wastage, lack of order fulfilment with every process being labor intensive and incomprehensive making warehouse operations inefficient.
♦ The challenges were exaggerated by speed and accuracy of inventory audits, reruns between warehouses and increased carbon footprint.
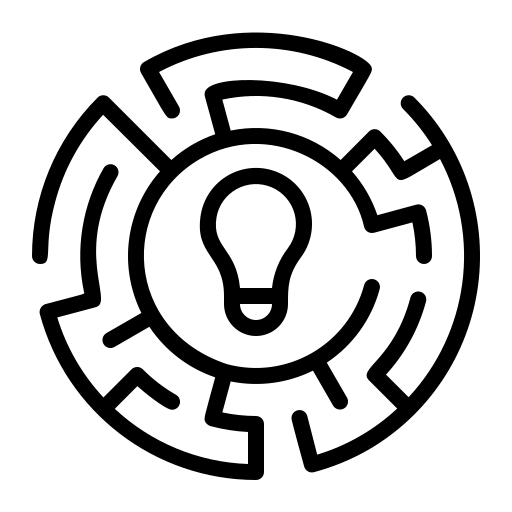
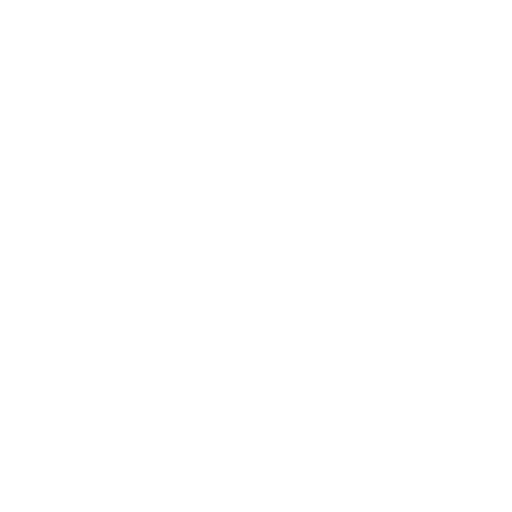
Intervention of Returnable Asset Tracking
♦ InThing Returnable Asset Tracking Solution was adopted to provide increased visibility and real time updates of their inventoried items and to monitor movement of items through doc-doors and selected doors.
♦ To monitor the movement of about 8,000 items through their Chicago warehouse, Inhabitr decided to utilize a innovative AI solution powered by cutting-edge sensors and AI-models trained for FF&E supply-chain.
♦ Integrated into the Inhabitr operational management system, the Returnable Asset Tracking Solution has the Periodic Inventory, Automated Outbound Audit Process, Asset Administration, Inventory Reconciliation, Preconfigured inventory and missing asset reports and Tag ID searches built into the system for rapid deployment.
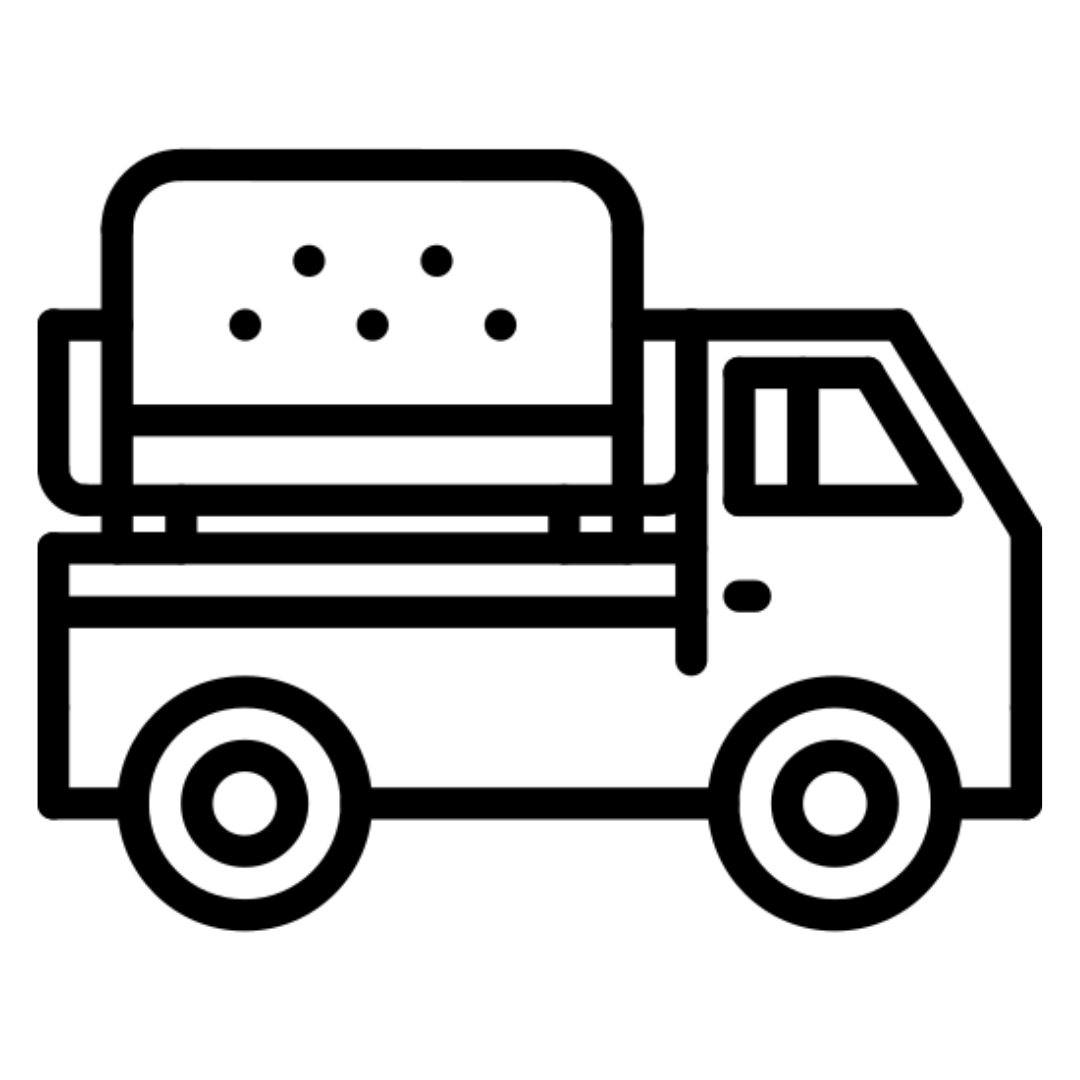
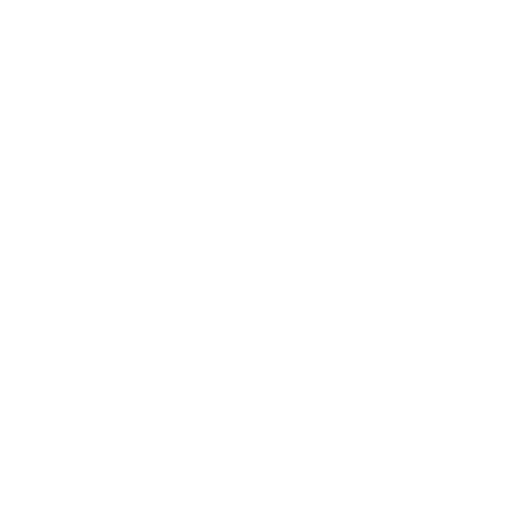
Unprecedented Furniture Goods Visibility
♦ Inhabitr used the Zebra-InThing solution in 2023 to monitor the movement of its furniture through warehouses. Using RFID tags, handheld RFID readers & Visium mobile, inbound and outbound movements of inventory through dock-doors was monitored, with updates and insights delivered realtime.
♦ The current manual processes was automated to deliver an optimal and scalable solution design, automating shipping receiving validations to prevent wrong shipments.
♦ InThing’s Returnable Asset Visibility Solution provided real-time inventory audit data, helped customers track the changes in their inventory cycle count, provided asset location whereabouts, and container and asset configuration management. Warehouse personnel could create containers and perform rapid audits of all items inside a box as a single kit.
How InThing Returnable Asset Tracking + RFID readers work
➤ Inhabitr will attach tags to all existing items and perform a onetime import into Visium. Items can be enrolled into Visium using the APIs, using the web application, or using a mobile device.
➤ Visium mobile application will be used to perform periodic inventory of items in relation to their location. RFID tags will be used to mark locations throughout the facility.
➤ For the Outbound Audit Process- Handheld, Inhabitr systems will use Visium API to create Customer & Work Order entities which can be viewed on the Visium frontend.
➤ For the Outbound Audit Process - Dock Door, all items staged for the specific work order will be audited at the dock door using RFID scans. This double verification minimizes human errors at the physical loading operation. A display application shows the loading process in real time to identify any exceptions and allow operators to perform corrective actions.
➤ The Returnable Asset Tracking solution reduces time wastage & re-runs between warehouses and customer locations to reduce the carbon footprint in transportation.
Disrupting the furniture-rental industry with cutting-edge AI
Providing unparalleled insights, flexibility, speed and cost efficiency in furniture retail management
View Other Success Stories
Browse through the work we've done with clients, partners and businesses across verticals and industries.
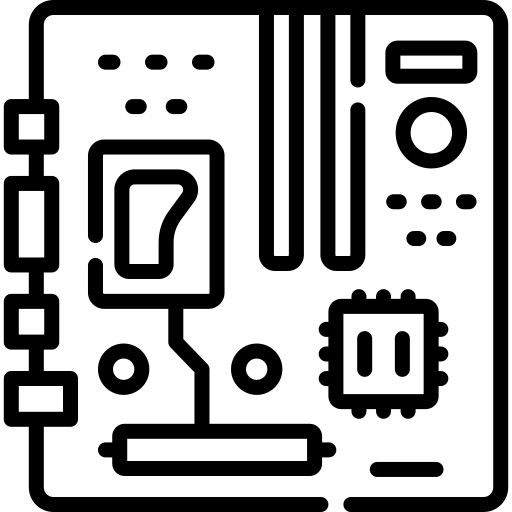
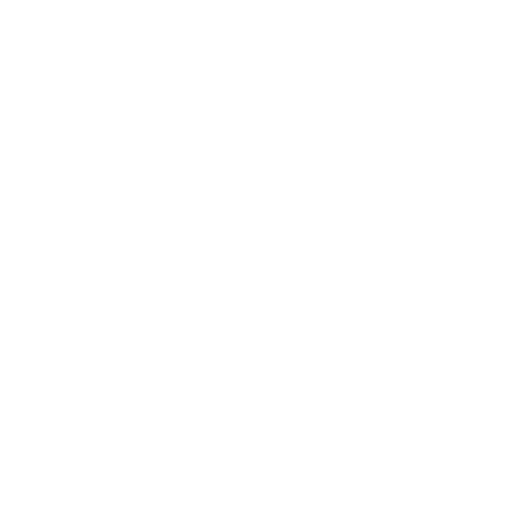
APPLIED MATERIALS INC.
Applied Materials is a leading global provider of equipment, services, and software to enable the manufacture of semiconductor, flat-panel display, and solar photovoltaic products. InThing's RFID-based asset visibility solution saves this hi-tech lab, $1M annually.
Know More